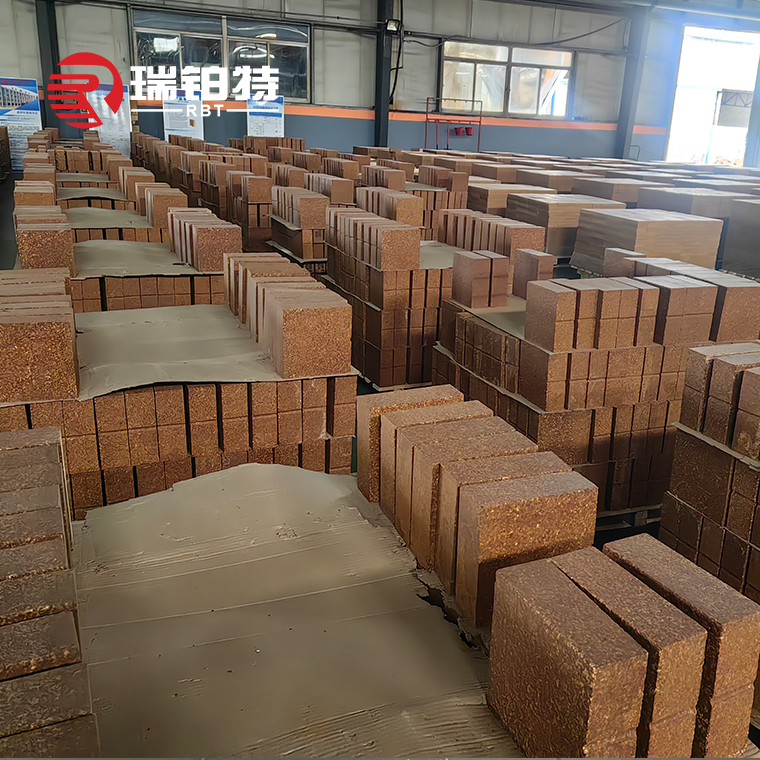
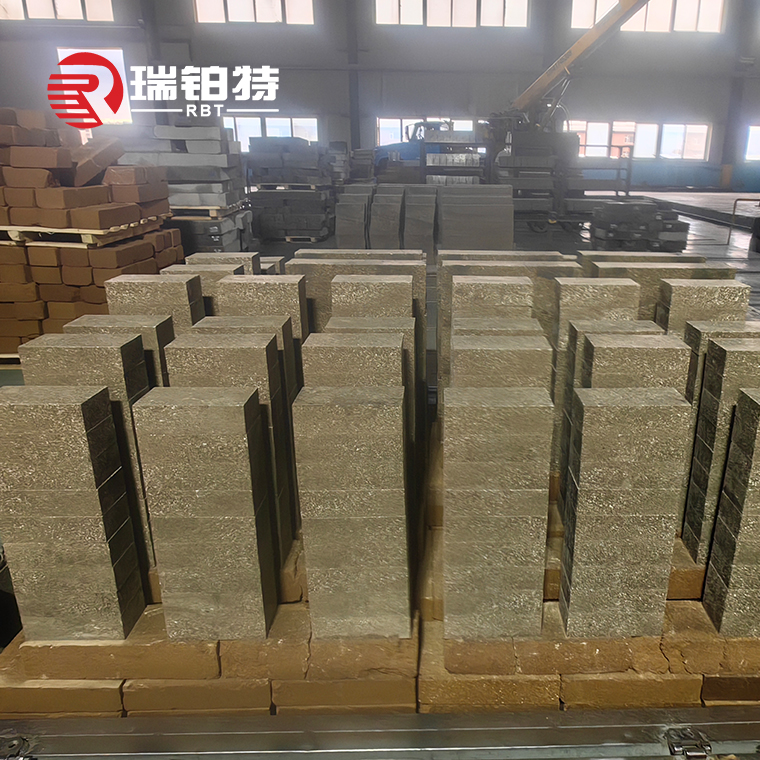
Dans le secteur industriel à haute température, la performance des matériaux de revêtement des fours a un impact direct sur l'efficacité de la production et la qualité des produits. Représentantes des matériaux réfractaires hautes performances, les briques de spinelle de magnésie-alumine, grâce à leurs excellentes propriétés globales, sont devenues le choix idéal pour les industries telles que l'acier, le verre et le ciment. Elles résistent à l'érosion à haute température et prolongent la durée de vie des équipements, offrant ainsi un soutien fiable à la production industrielle à haute température.
Leader de l'industrie avec des performances exceptionnelles
Les briques de spinelle de magnésie-alumine sont synthétisées à partir de magnésie et d'oxyde d'aluminium par des procédés spéciaux. Leur structure cristalline unique leur confère de puissants avantages en termes de performances. Ces briques présentent une résistance exceptionnelle aux températures extrêmes, pouvant atteindre 1 800 °C. Même exposées à des températures élevées prolongées, elles conservent des propriétés physiques et chimiques stables, prévenant ainsi efficacement les dommages causés aux revêtements des fours par les températures élevées.
La résistance aux chocs thermiques est une caractéristique remarquable des briques de spinelle de magnésie-alumine. Lors des cycles fréquents de chauffage et de refroidissement des fours, les matériaux réfractaires ordinaires sont sujets aux fissures et à l'écaillage dus aux contraintes thermiques. Cependant, grâce à leur faible coefficient de dilatation thermique et à leur bonne ténacité, les briques de spinelle de magnésie-alumine peuvent atténuer efficacement les impacts des contraintes thermiques, réduisant ainsi considérablement le risque de dommages par choc thermique, prolongeant ainsi la durée de vie et minimisant les temps d'arrêt du four pour maintenance.
Les briques de spinelle de magnésie-alumine offrent également une excellente protection contre l'érosion chimique. Elles présentent une excellente résistance aux scories alcalines et acides, ainsi qu'aux gaz à haute température, empêchant efficacement la pénétration de substances nocives et préservant la sécurité structurelle des fours. Que ce soit dans l'environnement fortement alcalin de la fusion de l'acier ou dans l'atmosphère acide et à haute température de la production de verre, elles assurent leur fonction protectrice de manière stable.
Applications approfondies dans de multiples secteurs
Dans l'industrie sidérurgique, les briques de spinelle de magnésie-alumine sont largement utilisées dans les convertisseurs, les poches de coulée et les répartiteurs. Lors de la fabrication de l'acier dans les convertisseurs, elles résistent à l'érosion et à l'érosion de l'acier fondu et des scories à haute température, garantissant ainsi l'intégrité du revêtement du convertisseur. Utilisées dans les poches de coulée et les répartiteurs, elles réduisent efficacement la réaction entre l'acier fondu et les matériaux de revêtement, améliorent la pureté de l'acier fondu et optimisent la qualité de l'acier. Après l'adoption des briques de spinelle de magnésie-alumine par une grande entreprise sidérurgique, la durée de vie de ses poches de coulée est passée de 60 à 120 coulées en moyenne, réduisant ainsi considérablement les coûts de production.
Dans l'industrie verrière, les briques de spinelle de magnésie-alumine sont des matériaux privilégiés pour les pièces clés des fours de fusion du verre. Dans les points chauds et les régénérateurs des fours de fusion du verre, elles résistent à l'érosion du verre fondu à haute température et au décapage des gaz à haute température, préservant ainsi la stabilité structurelle du four, réduisant la fréquence de maintenance et améliorant la continuité et la stabilité de la production de verre. L'utilisation de briques de spinelle de magnésie-alumine permet de prolonger le cycle de révision des fours de verre de 2 à 3 ans, améliorant ainsi les retombées économiques des entreprises.
Lors de la production de ciment, l'environnement à haute température des fours rotatifs impose des exigences strictes aux matériaux réfractaires. Grâce à leur résistance aux hautes températures, à l'abrasion et à leur bonne stabilité chimique, les briques de spinelle magnésie-alumine jouent un rôle crucial dans la zone de transition et la zone de cuisson des fours rotatifs. Elles assurent le fonctionnement stable du corps du four sous haute température et forte charge, contribuant ainsi à l'augmentation de la production et à l'amélioration de la qualité du ciment.
Guide d'achat professionnel
Lors du choix des briques de spinelle magnésie-alumine, les points clés suivants doivent être pris en compte : premièrement, prêter attention à la composition chimique et minérale des matériaux. L'utilisation de magnésie et d'oxyde d'aluminium de haute pureté garantit la stabilité des performances des briques. Deuxièmement, il faut se concentrer sur les indicateurs de performance physique des produits, tels que la masse volumique apparente, la porosité apparente et la résistance à l'écrasement à froid à température ambiante. Ces indicateurs reflètent directement la qualité et la durabilité des briques. Troisièmement, il faut évaluer le processus de production et le système de contrôle qualité des fournisseurs. Privilégiez des fournisseurs dotés d'équipements de production de pointe, de processus d'inspection complets et d'une riche expérience industrielle pour garantir la fiabilité de la qualité des produits. De plus, en fonction des conditions d'exploitation spécifiques, la précision dimensionnelle et l'adaptabilité de la forme des briques doivent également être prises en compte pour garantir une construction et une installation fluides.
Grâce à leurs performances exceptionnelles et à leurs nombreuses applications, les briques de spinelle magnésie-alumine sont devenues des matériaux réfractaires hautes performances indispensables dans les industries à haute température. Qu'il s'agisse d'améliorer l'efficacité de la production, de réduire les coûts ou de garantir la qualité des produits, elles offrent des solutions fiables aux entreprises. Contactez-nous dès maintenant pour obtenir des informations professionnelles sur nos produits et des services personnalisés, et laissez-nous sécuriser votre production industrielle à haute température !
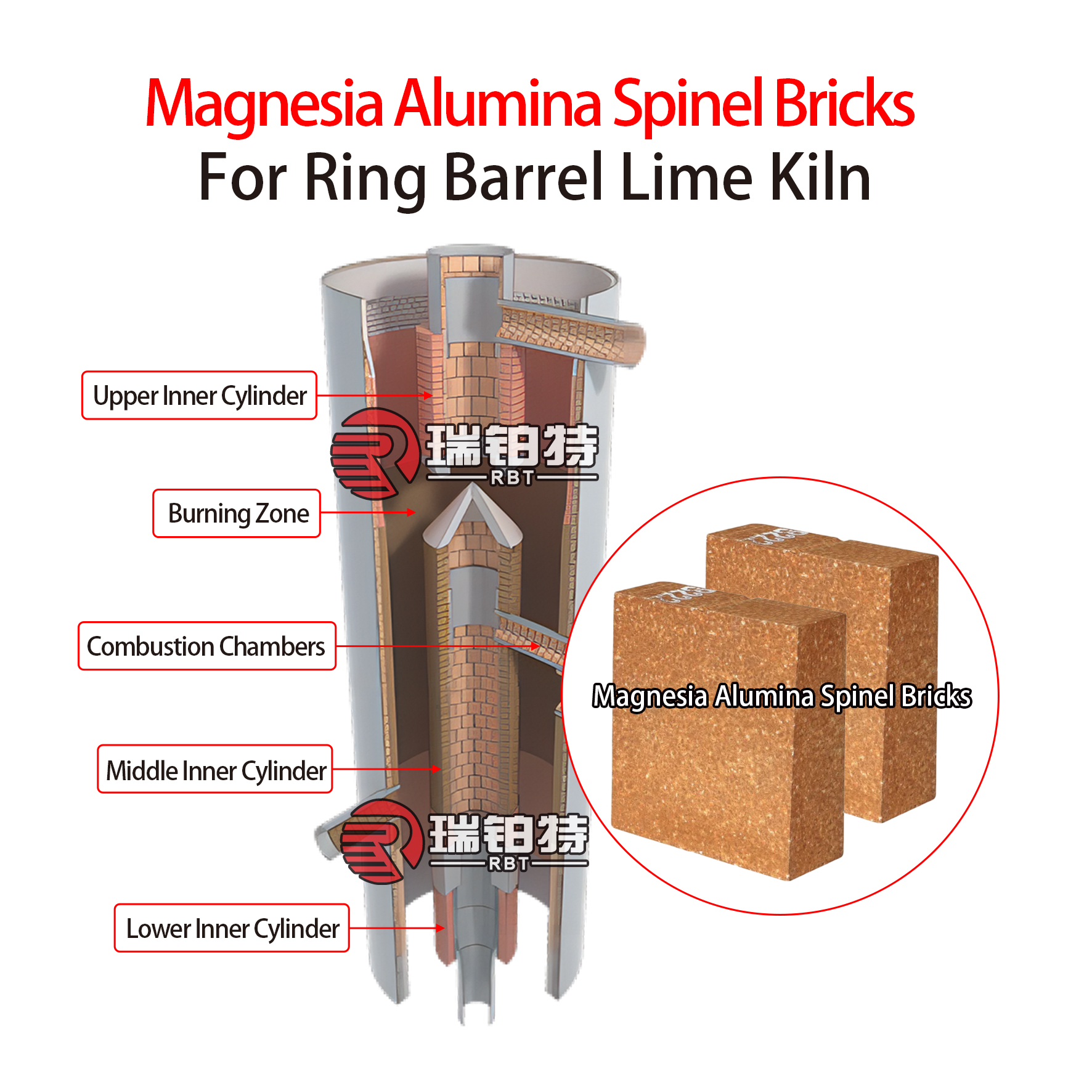
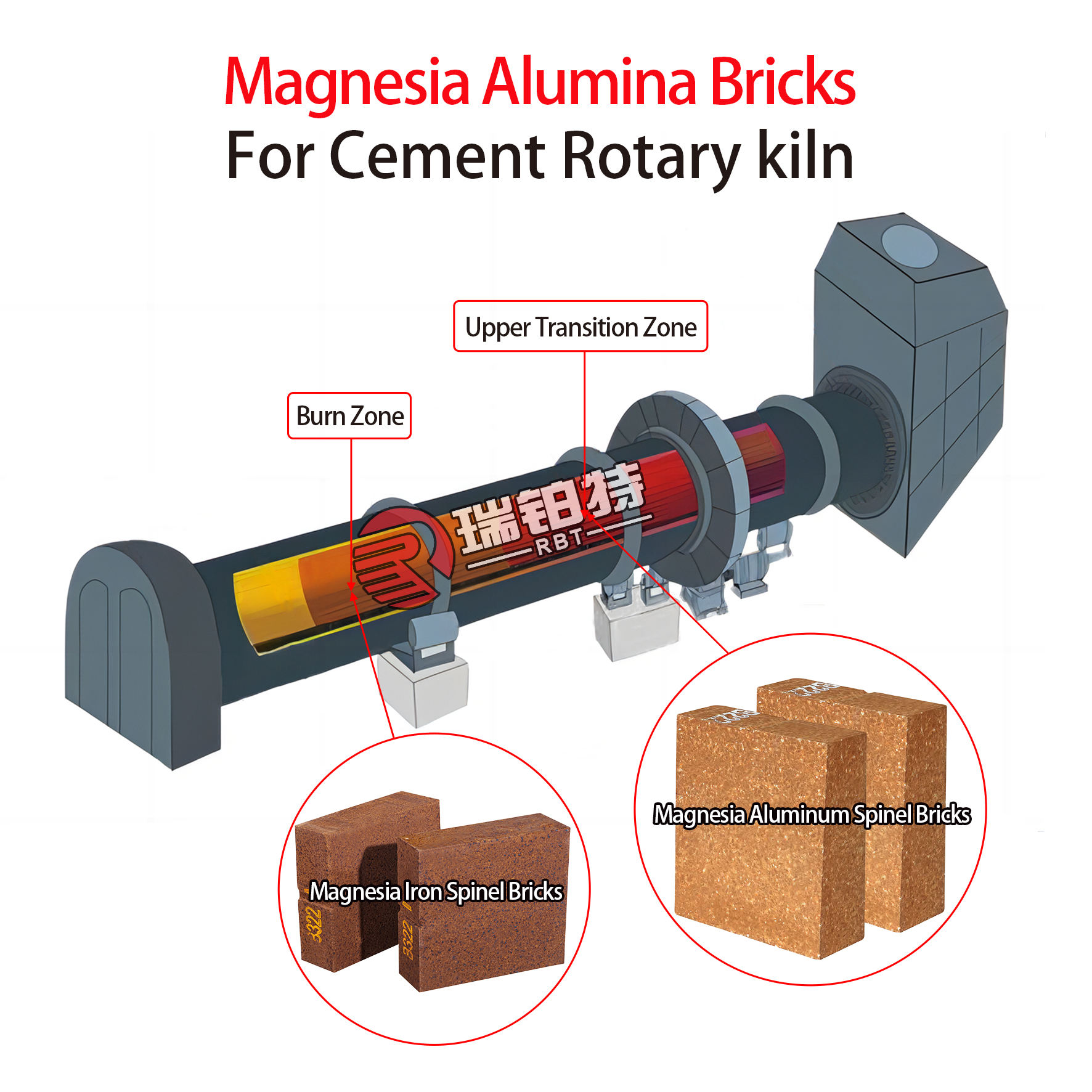
Date de publication : 23 juin 2025