Les avantages des briques de magnésie-carbone sont :Résistance à l'érosion par les scories et bonne résistance aux chocs thermiques. Auparavant, les briques MgO-Cr2O3 et les briques en dolomie présentaient l'inconvénient d'absorber les composants des scories, ce qui entraînait un écaillage structurel et des dommages prématurés. Grâce à l'ajout de graphite, les briques en magnésie-carbone ont éliminé cet inconvénient. Leur particularité est que les scories ne pénètrent que dans la surface de travail, limitant ainsi l'écaillage de la structure et lui conférant une longue durée de vie.
Désormais, en plus des briques traditionnelles en magnésie-carbone liées à l'asphalte et à la résine (y compris les briques de magnésie imprégnées d'huile cuite),les briques de magnésie-carbone vendues sur le marché comprennent:
(1) Briques de carbone magnésien constituées de magnésie contenant 96 % à 97 % de MgO et de graphite 94 % à 95 % de C ;
(2) Briques de carbone magnésien constituées de magnésie contenant 97,5 % ~ 98,5 % de MgO et de graphite 96 % ~ 97 % de C ;
(3) Briques de carbone magnésien fabriquées à partir de magnésie contenant 98,5 % à 99 % de MgO et 98 % à 99 % de graphite.
Selon la teneur en carbone, les briques de carbone magnésien sont divisées en :
(I) Briques de magnésie imprégnées d'huile cuite (teneur en carbone inférieure à 2 %) ;
(2) Briques de magnésie liées au carbone (teneur en carbone inférieure à 7 %) ;
(3) Briques de magnésie-carbone liées à la résine synthétique (teneur en carbone de 8 à 20 %, jusqu'à 25 % dans certains cas). Des antioxydants sont souvent ajoutés aux briques de magnésie-carbone liées à l'asphalte et à la résine (teneur en carbone de 8 à 20 %).
Les briques de carbone magnésien sont produites en combinant du sable MgO de haute pureté avec du graphite écailleux, du noir de carbone, etc. Le processus de fabrication comprend les étapes suivantes : concassage, criblage, calibrage et mélange des matières premières en fonction de la formule et des performances de prise du produit. La température de l'agent est portée à près de 100 à 200 °C, puis malaxée avec le liant pour obtenir la boue MgO-C (mélange cru). La boue MgO-C, à base de résine synthétique (principalement phénolique), est moulée à froid ; la boue MgO-C, combinée à de l'asphalte (chauffé à l'état fluide), est moulée à chaud (environ 100 °C). Selon la taille du lot et les exigences de performance des produits MgO-C, des équipements de vibration sous vide, des équipements de moulage par compression, des extrudeuses, des presses isostatiques, des presses à chaud, des équipements de chauffage et des équipements de compactage peuvent être utilisés pour traiter les boues MgO-C. à la forme idéale. Le corps MgO-C formé est placé dans un four à 700-1200 °C pour un traitement thermique visant à convertir le liant en carbone (ce processus est appelé carbonisation). Afin d'augmenter la densité des briques de magnésie-carbone et de renforcer la liaison, des charges similaires aux liants peuvent également être utilisées pour imprégner les briques.
De nos jours, la résine synthétique (en particulier la résine phénolique) est principalement utilisée comme liant des briques de magnésie-carbone.L'utilisation de briques de magnésie-carbone liées à la résine synthétique présente les avantages fondamentaux suivants :
(1) Les aspects environnementaux permettent la transformation et la production de ces produits ;
(2) Le processus de production de produits dans des conditions de mélange à froid permet d’économiser de l’énergie ;
(3) Le produit peut être traité dans des conditions de non-durcissement ;
(4) Comparé au liant bitumineux, il n'y a pas de phase plastique ;
(5) Une teneur en carbone accrue (plus de graphite ou de charbon bitumineux) peut améliorer la résistance à l'usure et la résistance aux scories.
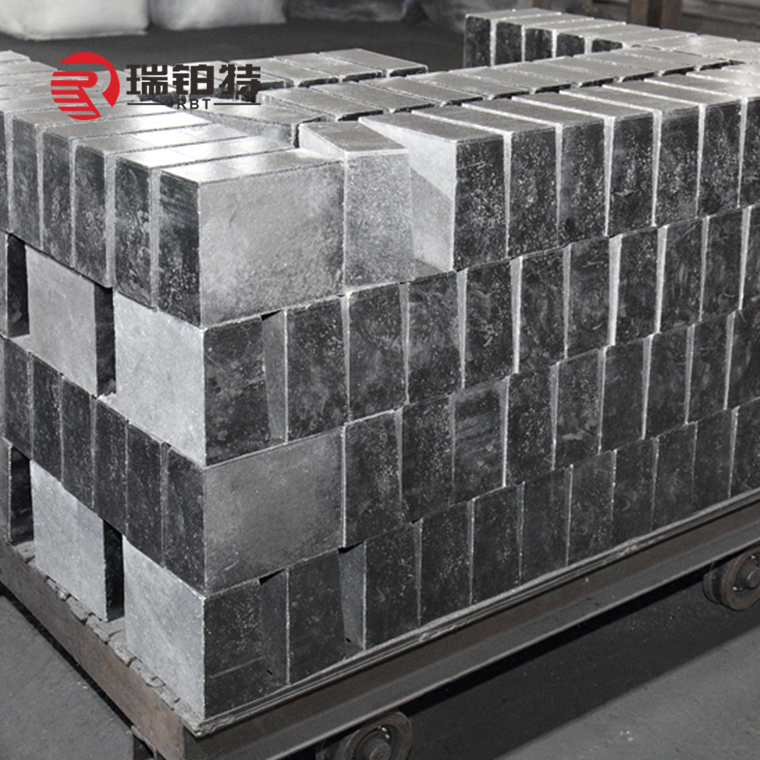
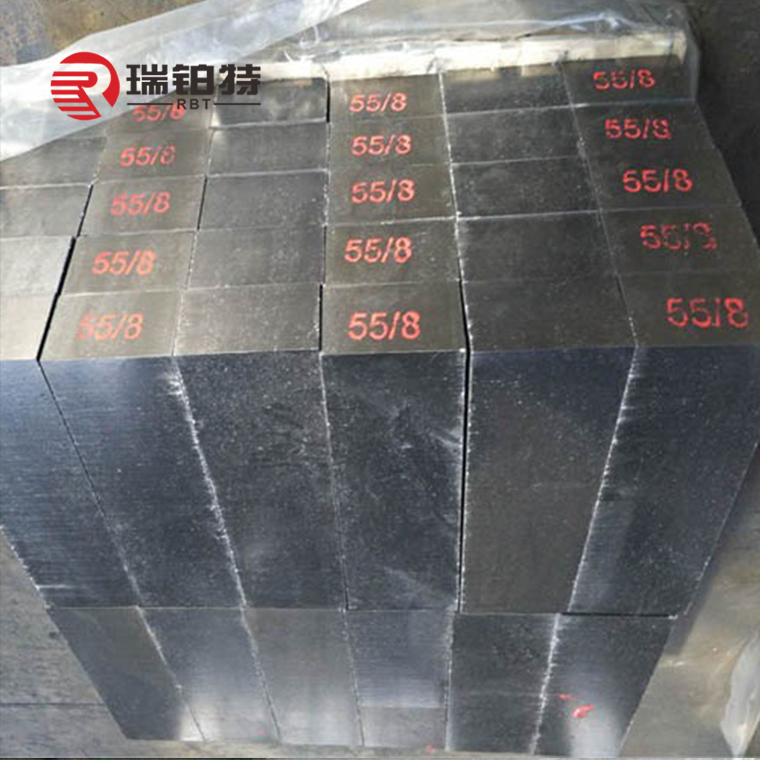
Date de publication : 23 février 2024